In the realm of wire coatings, the choice of material plays a pivotal role in ensuring durability, protection, and overall performance. One material that has gained significant traction in recent years is polyurethane wire enamel. Known for its exceptional properties and versatility, polyurethane enamel has become a go-to solution for a wide range of applications. In this blog post, we will explore the numerous advantages of polyurethane wire enamel, shedding light on why it has become a popular choice for wire coating.
Outstanding Electrical Insulation PropertiesOne of the primary reasons for the widespread use of polyurethane wire enamel is its exceptional electrical insulation properties. This material exhibits high dielectric strength and low dissipation factor, making it ideal for applications where electrical conductivity must be minimized. Whether used in transformers, motors, or electronic devices, polyurethane enamel ensures reliable insulation, preventing electrical leakage and enhancing overall safety.
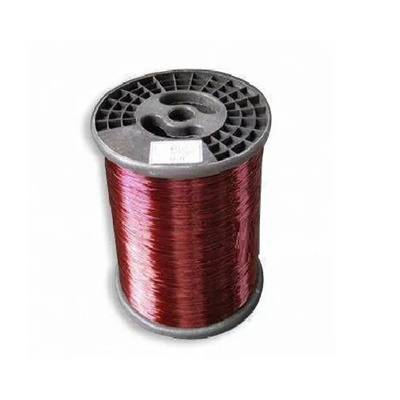
Resistance to Environmental Factors
Polyurethane enameled wire excels in withstanding a wide range of environmental factors. It is highly resistant to moisture, chemicals, and abrasion. This makes it an excellent choice for applications that are exposed to harsh environments, such as outdoor installations or industrial settings where exposure to chemicals is common. The robust nature of polyurethane enamel ensures that the wire remains protected and functional even in demanding conditions.
Flexibility and Durability
Flexibility is a crucial consideration when it comes to wire coatings. Polyurethane enamel exhibits remarkable flexibility, allowing the wire to bend and twist without compromising the integrity of the coating. This property is particularly valuable in applications where wires may be subject to movement or vibration. Additionally, polyurethane enamel is highly durable, providing long-lasting protection against wear and tear.
Thermal Stability
In applications where wires are exposed to elevated temperatures, the thermal stability of the wire coating is of paramount importance. Polyurethane enamel boasts impressive resistance to high temperatures, ensuring that it maintains its protective properties even in extreme heat. This makes it an excellent choice for applications in industries such as automotive, aerospace, and electronics, where exposure to high temperatures is common.
Low VOC Emissions
With increasing emphasis on environmental sustainability, the use of low-VOC (Volatile Organic Compounds) materials has become a priority. Polyurethane wire enamel aligns with this trend, as it typically emits low levels of VOCs during application. This makes it an eco-friendly choice for wire coating applications, reducing the environmental impact associated with the manufacturing process.
Versatility in Application
Polyurethane wire enamel can be applied using various methods, including dipping, spraying, or brushing. This versatility in application methods allows for flexibility in choosing the most suitable technique for a specific project. Whether it's a large-scale industrial application or a smaller-scale project, polyurethane enamel can be tailored to meet the specific requirements of the job.
ConclusionPolyurethane wire enamel stands as a versatile and reliable choice for wire coating applications. With its outstanding electrical insulation properties, resistance to environmental factors, flexibility, durability, thermal stability, and low VOC emissions, it has become a preferred option across a wide range of industries. By choosing polyurethane enamel, manufacturers can ensure that their wires are protected, reliable, and built to withstand the challenges of demanding environments.