Magnet wire is a crucial component commonly found in electrical equipment. However, failures can occur during its usage. This article aims to outline the common signs to identify magnet wire failures and provide effective methods for prevention.
Magnet wire is an indispensable component in modern electrical devices, widely used in motors, transformers, generators, and more. However, due to prolonged operation, environmental factors, and manufacturing quality, magnet wire can experience failures. Early identification and prevention of these failures are essential for the smooth operation of equipment. This article will discuss the common signs to identify magnet wire failures and provide effective methods for prevention.
Identifying Common Signs of Magnet Wire Failures:
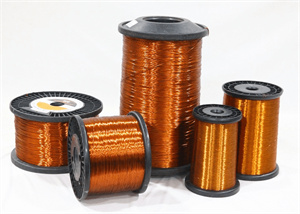
Temperature rise: When magnet wire fails, its internal resistance may increase, resulting in the generation of excess heat during current flow. Therefore, if you notice an abnormal temperature rise on the surface of the magnet wire, it could be a sign of failure.
Coil short-circuits: Coil short-circuits are a common issue in magnet wire failures. When a short-circuit occurs between two or more coils, the current may bypass the normal path, leading to improper equipment operation. Measuring resistance or using infrared thermography to detect coil short-circuits is an effective method for identifying this failure.
Insulation damage: The insulation layer of
magnet wire plays a crucial role in protecting the conductors. If the insulation layer is damaged, the conductors may come into contact with other metal components, resulting in short-circuits or current leakage. Regularly inspect the integrity of the insulation layer, especially in humid or corrosive environments.
Resistance changes: The resistance of magnet wire is typically fixed, but when failures occur, resistance may change. Regularly measuring the resistance of magnet wire can help detect potential failures early on.
Methods to Prevent Magnet Wire Failures:
Quality control: Choose reputable magnet wire suppliers and ensure that the wire used meets relevant standards and specifications. Conduct regular quality checks and ensure that the manufacturing process adheres to best practices.
Environmental monitoring: Install equipment in suitable environments, avoiding exposure to excessive temperatures, humidity, or corrosive gases. Regularly inspect the environmental conditions around the equipment and take necessary measures to protect the magnet wire from adverse environmental effects.
Regular maintenance: Regularly inspect the condition of the magnet wire, including temperature, resistance, and integrity of the insulation layer. For high-risk equipment, it is recommended to establish a maintenance schedule and conduct regular checks and maintenance accordingly.
Overload protection: Design equipment with appropriate rated current and power to avoid overload operation. Utilize suitable overload protection devices such as fuses or circuit breakers to prevent magnet wire damage from overloading.
Conclusion:
Magnet wire failures significantly impact the normal operation and safety of electrical equipment. By identifying the common signs of magnet wire failures and implementing preventive measures, the occurrence of failures can be effectively reduced. Quality control, environmental monitoring, regular maintenance, and overload protection are key measures for preventing magnet wire failures. By employing these methods correctly, the lifespan of magnet wire can be maximized, ensuring the stable operation of equipment.
In conclusion, identifying and preventing magnet wire failures require maintenance personnel to possess adequate knowledge and skills. Regular maintenance and inspections can help detect potential failures and take timely measures for repair or replacement. Proper usage and protection of magnet wire contribute to improved reliability and safety of equipment, extended lifespan, reduced maintenance costs, and ensured continuity and stability in production processes.