Electric motors are ubiquitous in modern life, powering everything from industrial machinery to household appliances. However, the initial surge of current, known as starting current, can be a challenge to manage. Excessive starting current can lead to voltage drops, increased wear and tear, and even damage to the motor itself. In this blog, we'll delve into the methods used to reduce starting current, ensuring efficient and smooth motor operation.
Starting current, also called inrush current, is the brief surge of electricity that flows through a motor when it's switched on. This current can be several times higher than the motor's rated running current. While this initial jolt is necessary to overcome inertia and initiate rotation, it can strain the electrical system and components.
Methods to Reduce Starting CurrentDirect-On-Line (DOL) Starters:
The simplest method is using a Direct-On-Line starter, which directly connects the motor to the power source. While easy to implement, this approach causes a high inrush current due to the absence of any current-limiting elements.
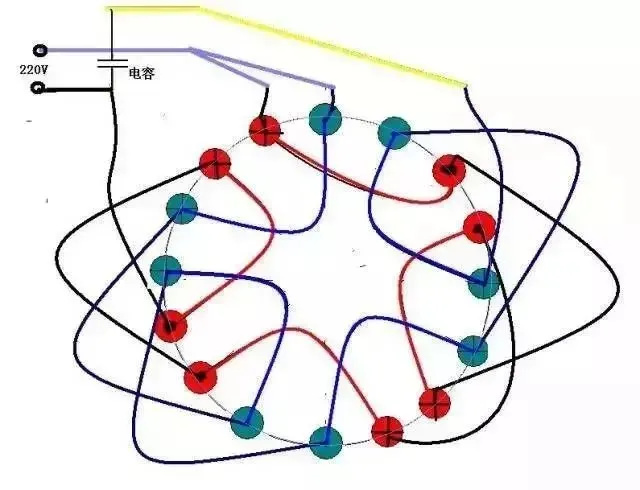
Soft Starters:
Soft starters are electronic devices that gradually ramp up the voltage supplied to the motor during startup. This controlled acceleration reduces the starting current and minimizes mechanical stress on the motor and connected machinery. Soft starters find extensive use in applications where abrupt starts could damage equipment.
Star-Delta Starters:
In this method, the motor is initially connected in a 'star' configuration, reducing the applied voltage by a factor of 1/√3. After a preset time, the connection shifts to a 'delta' configuration, applying full voltage. This approach limits the starting current but compromises the torque output during startup.
Variable Frequency Drives (VFDs):
VFDs, also known as inverters, provide the most versatile solution for reducing starting current. They control the motor's frequency and voltage, allowing a gradual increase in speed and torque during startup. VFDs enable energy-efficient operations, precise control, and can be programmed to match the specific requirements of the motor.
Auto-Transformer Starters:
Auto-transformers are used to temporarily reduce the voltage applied to the motor during startup. As the motor gains speed, the auto-transformer adjusts the voltage levels to the rated voltage. This approach minimizes the inrush current while maintaining torque output.
Rotor Resistance Starters:
Primarily used in slip-ring induction motors, rotor resistance starters insert external resistors in the rotor circuit during startup. These resistors are gradually bypassed as the motor accelerates, reducing the initial current surge.
Benefits of Reducing Starting CurrentImproved System Reliability:
By limiting the starting current, you can prevent voltage drops, which can otherwise affect other connected equipment and cause instability in the electrical system.
Extended Motor Life:
Reducing the mechanical and electrical stress during startup helps prolong the motor's lifespan, minimizing wear and tear.
Energy Efficiency:
Methods like VFDs allow motors to start and operate at optimal speeds, resulting in energy savings over time.
Process Optimization:
In industrial settings, smoother startups can lead to better process control and reduced downtime.
ConclusionThe various methods to reduce starting current play a crucial role in ensuring the efficient and reliable operation of electric motors. Selecting the appropriate method depends on factors such as the motor type, application, and operational requirements. As technology advances, the development of more sophisticated and efficient solutions continues to enhance motor efficiency while minimizing the impact of starting current on electrical systems. By carefully considering these methods, engineers and operators can strike a balance between efficient motor operation and reduced stress on the electrical infrastructure.