Copper and aluminum wires are common conductive materials that are often used to transmit power and signals in electrical and electronic applications. Although they can both be used to connect circuits and devices, copper and aluminum wires are connected in different ways due to their different physical and chemical properties.
Brazing: Brazing is a common method of joining copper wires. It involves joining two copper wires directly together using solder and solder paste. During the hard soldering process, you need to use a heating tool (such as a soldering gun) to heat the solder to the melting temperature and apply it to the parts where the copper wires contact. Once the solder cools and solidifies, a solid connection is formed.
Soft soldering: For aluminum wire connections, traditional hard soldering methods are not suitable because the chemical reaction between the aluminum wire and the solder will cause the connection to be unreliable. Therefore, soft soldering or aluminum wire connectors are often used. Soft welding involves the use of specially designed aluminum electrodes or wires that have better compatibility with aluminum wire. In soft welding, an aluminum electrode or wire is heated to melting temperature and then applied to the parts where the aluminum wire contacts. The solder material cools and forms a reliable connection.
Crimping: Crimping is a common method of joining copper and aluminum wire that does not involve soldering or the use of other connecting agents. Crimping uses a special crimping tool to place the copper and aluminum wires together into the connector and then connect them tightly together by applying sufficient pressure. This method is commonly used for power transmission lines and cable connections.
Plug-in connection: Plug-in connection is a simple method in which copper and aluminum wires are connected together using plug-in terminals or plugs. These terminals typically have copper and aluminum contact surfaces to ensure good conductivity and reliability. Plug-in connections are suitable where frequent disassembly and reconnection are required.
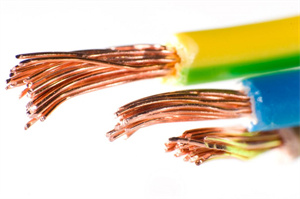
Conductive grease: Due to the potential difference and oxidation problems between aluminum wires and copper wires, the use of conductive grease can improve the contact and conductive properties between them. Conductive grease often contains silver or other conductive materials that fill tiny gaps and provide better contact.
Electrolytic plating: Electrolytic plating is a method of depositing a copper layer or other metal layer on the surface of aluminum wires to improve the conductivity and corrosion resistance of the aluminum wires. Copper plating can form a protective layer on the surface of aluminum wires, providing better connection performance.
Specialty connectors: Some manufacturers offer connectors specifically designed to connect copper and aluminum wires. These connectors usually use special materials and designs to ensure reliable connections between copper and aluminum wires and solve problems caused by thermal expansion and contraction.
It should be noted that due to the different thermal expansion and contraction coefficients of
enameled aluminum wires and copper wires, they may be affected by thermal expansion and contraction after connection. This may cause the connection to loosen or break. Therefore, in practical applications, special design and process measures need to be taken when connecting aluminum wires and copper wires to ensure a stable and reliable connection.
Temperature and current capacity considerations: When connecting copper and aluminum wires, there are current capacity and temperature characteristics that need to be considered. Since the conductivity of aluminum wire is lower than that of copper wire, aluminum wire will generate higher resistance and heat under the same current load. Therefore, when designing and selecting cables and connectors, make sure they can withstand the expected current loads and have adequate heat dissipation capabilities.
In general, connecting copper and aluminum wires requires special techniques and precautions to ensure stable connections and reliable conductive performance. In practical applications, it is recommended to refer to the manufacturer's guidelines and recommendations to select appropriate connection methods and materials, as well as to take necessary precautions to solve problems that may arise when connecting copper and aluminum wires.